Table of Contents
In 1981, regular maintenance checks revealed that the wrought iron supports on the Statue of Liberty’s interior were affected by a startling quantity of rust. The cause was not simply the saltwater surrounding Liberty Island, but a reaction between the iron armatures and the copper skin of the statue itself. The gradual breakdown of a protective layer of shellac had amounted to a major case of galvanic corrosion between two incompatible metals.
Galvanic corrosion is a natural electrochemical process that occurs when two materials with dissimilar electrode potentials are left in contact with one another. When an electrolyte is present, such as sodium or chloride particles in the air, one metal will act as an anode and the other will act as a cathode. This is the same principle that enables carbon-zinc cell batteries to work. In the case of structural applications, however, it’s very undesirable and no small issue to fix. Apart from the Statue of Liberty, which needed an extensive renovation, another recent notable case of galvanic corrosion affected the USS Independence, where the combination of seawater, the ship’s aluminum hull, and its stainless steel jet propulsion system led to major structural integrity problems.
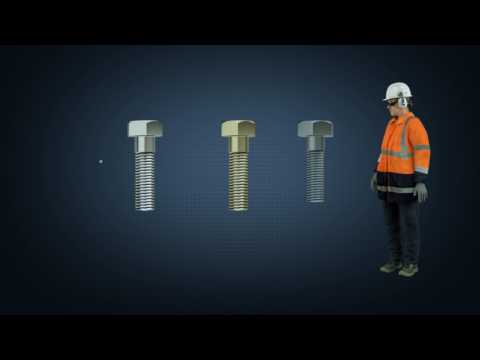
If this type of corrosion can occur in structures as iconic as the Statue of Liberty or a lead ship of the U.S Navy, what does this mean for everyday applications? Is galvanic corrosion inevitable unless all materials in a structure are homogenous? Are stainless steel washers the right choice for an aluminum structure? Can bronze hardware be secured with brass screws? These questions can be addressed by examining the causes of this natural process.
What Causes Galvanic Corrosion?
Galvanic corrosion occurs not simply because two different metals are left in contact. The potential for this type of reaction and its rate all depends on electrical conductivity and whether one material will act as an anode and the other as a cathode. An anode and cathode combination enables ions to migrate via the presence of an electrolyte. The interaction then stops the build-up of an electrical charge that normally amounts to natural corrosion resistance and the result is the deterioration of the material acting as the anode.
The effects of this natural process can be detrimental. Fortunately, galvanic corrosion can be easily avoided through a few simple practices and a little bit of foresight.
Preventing Galvanic Corrosion
The first way to avoid galvanic corrosion is to use compatible materials or those that will not permit ion migration if an electrolyte is present. Humidity, saltwater particles, and even temperature changes, can all function in such a way, so the environment will have a significant effect.
When evaluating the relationship between two metals and the presence of an electrolyte, a galvanic corrosion chart or table serves as a handy reference. These graphs are usually color-coded or shaded to show whether a material is more likely to function as a cathode or an anode and whether galvanic corrosion will occur when they are in direct contact.
If for example, the intent was to use 18/8 stainless steel washers and bolts on copper cookware, a galvanic corrosion chart will show this pairing would be likely to foster corrosion, especially if it’s used with any sort of food containing salt, calcium, potassium, etc. If however, that same type of fastener assembly or other 300 series stainless steel washers and bolts were used with cast iron, galvanic corrosion would not be likely to occur even with the electrolytes present.
But what happens when two different grades of the same metal are in contact? Will using 18/10 stainless steel screws with 17/4 stainless steel washers foster galvanic corrosion? Fortunately, there is little potential for such as reaction across different grades of the same material.
Even when mixing potentially reactive metals, galvanic corrosion can be prevented if the right powered anode rod is employed and maintained. In the case of the Statue of Liberty, the problem did not occur sooner thanks to an insulating layer of shellac, which simply wore down over time. As long as such protections are maintained, they are effective.
Electroplating or galvanization, zinc-coating, and other treatments can reliably insulate materials and prevent the migration of ions. However, it’s very important that issues like abrasion are prevented. Even a simple scratch can be enough to wear away a layer of electroplating and create a material venerability.
Another option is to use non-metal buffers. High-strength fasteners and washers made from materials like HDPE or nylon can prevent galvanic corrosion and other forms of deterioration in many structures and equipment.
Read More on KulFiy