Table of Contents
Ever wondered what it takes to craft a perfect impeller for a pump or turbine? If you’re into machining or engineering, impeller machining might just be your next fascination! It’s a process that combines precision, smart material choices, and the right tools to create components that keep industries moving. In this guide, we’ll explore everything you need to know about impeller machining—starting with how to pick the best materials and tools.
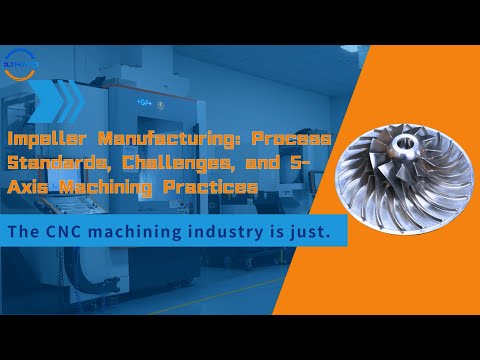
What Is Impeller Machining?
Impeller machining is the art and science of shaping impellers—those spinning parts that push fluids or gases in systems like pumps, compressors, and marine propellers. It often involves advanced techniques like 5-axis CNC machining to tackle the complex curves and tight tolerances of impeller designs. A well-machined impeller boosts efficiency and durability, but it all starts with the right foundation: materials and tools.
Choosing the Right Materials for Impeller Machining
Picking the perfect material is step one in impeller machining. The material you choose impacts performance, cost, and ease of machining. Here’s a quick look at the top contenders:
Stainless Steel: A favorite for its corrosion resistance, stainless steel suits impellers in water pumps or harsh environments. It’s tough but can wear tools down fast.
Aluminum: Lightweight and easy to machine, aluminum works great for low-stress applications like HVAC impellers. It’s less durable in extreme conditions, though.
Titanium: Perfect for high-performance impellers in aerospace or marine systems, titanium is strong and corrosion-resistant but pricey and hard to machine.
Bronze: Often used in marine impellers, bronze resists saltwater damage and offers good wear properties.
When choosing materials for impeller machining, think about the impeller’s job—will it face corrosive fluids or high pressure? Matching the material to the task is key. For instance, Thomasnet notes that stainless steel and titanium are popular for their reliability in tough settings.
Selecting the Best Tools for Impeller Machining
With your material in hand, it’s time to pick the tools that’ll bring your impeller to life. The intricate shapes of impellers demand precision equipment. Here’s what you’ll need:
CNC Machines
5-axis CNC machines are the go-to for impeller machining. They move in multiple directions at once, making them ideal for carving complex blade shapes. Cutting Tool Engineering highlights how 5-axis machining cuts down on tool wear and improves surface finish—crucial for impeller quality.
Cutting Tools
Carbide End Mills: Tough and versatile, these handle hard materials like stainless steel or titanium. Use them for roughing and finishing.
Ball Nose Cutters: Great for shaping curved impeller blades, ensuring smooth contours.
High-Speed Steel (HSS) Tools: Budget-friendly for softer materials like aluminum, but they wear out faster on tougher alloys.
Tool Enhancements
Coatings like Titanium Nitride (TiN) can boost tool life and reduce friction, especially in high-speed impeller machining.
The Impeller Machining Process
The impeller machining process involves crafting precision components for pumps and turbines using advanced techniques like 5-axis CNC machining. It starts with designing the impeller via CAD, followed by rough machining to shape the material—often stainless steel or titanium. Next, finishing refines the blades and surfaces, ensuring tight tolerances. Tools like carbide end mills and ball nose cutters are key. Finally, inspection verifies quality. This process demands skill and the right equipment for optimal performance.
Challenges in Impeller Machining
Impeller machining isn’t without hurdles:
Complex Shapes: Curved blades and tight spaces challenge tool access.
Tool Wear: Hard materials like titanium eat through tools quickly.
Precision: Tolerances as small as ±0.001 inches demand top-notch equipment and skill.
Using coated tools and regular maintenance can help tackle these issues.
Tips to Elevate Your Impeller Machining
High-Speed Machining: Speeds up the process and enhances finishes.
Smart Tool Paths: Software like CAMWorks can optimize paths for efficiency.
Prototype First: Test a small run to perfect your setup.
Conclusion
Impeller machining is a rewarding challenge that hinges on smart choices—picking the right materials like stainless steel or titanium, and tools like 5-axis CNC machines and carbide cutters. By mastering the process, you can craft impellers that excel in performance and longevity. Ready to start your next impeller machining project? Use this guide as your roadmap and watch your skills take off! Check out SimScale or Cutting Tool Engineering for more tips to keep you ahead.